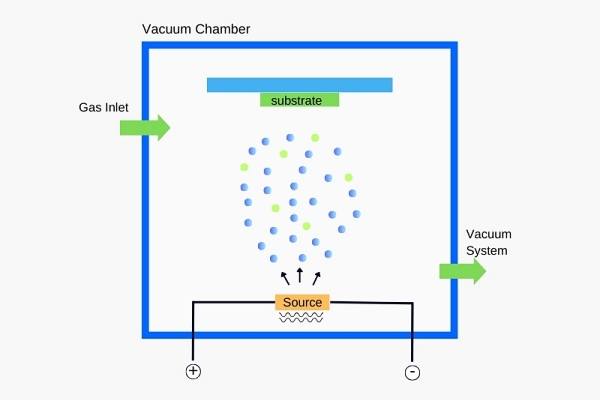
PVD Coating
PVD (Physical Vapor Deposition) technology refers to a technology that uses physical methods under vacuum conditions to vaporize material sources into gaseous atoms or molecules, or partially ionize them into ions, and deposit a thin film with certain special functions on the surface of a substrate.
PVD technology is a surface treatment technology that is widely used in various industries for material surface modification, functionalization, and decoration.
The main methods of physical vapor deposition include:
› Vacuum evaporation
› Sputtering coating
› Arc plasma coating
› Ion coating
We provide consumables and spare parts for thermal evaporation deposition and electron beam evaporation deposition, including electron beam crucible liners, tungsten evaporation filaments, electron gun tungsten filaments, boats, evaporation materials, etc.
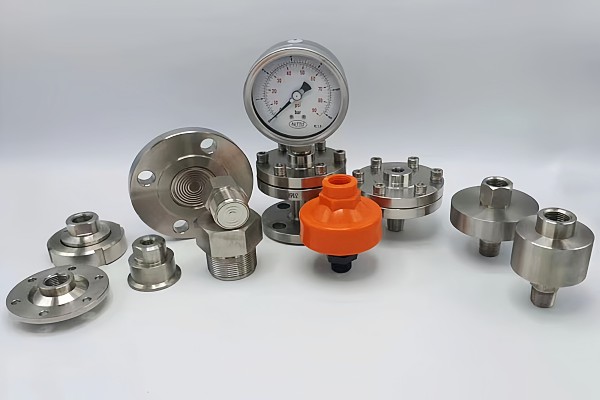
Instrument Spare Parts
WINNERS METALS provides customized spare parts for pressure, temperature, flow and other measurement instruments, including materials such as 316 stainless steel, Hastelloy, titanium, tantalum, etc.
These spare parts include:
› Flowmeter electrodes, grounding rings, etc.
› Diaphragm seals, flushing rings, metal diaphragms, etc. for pressure measurement systems.
› Thermocouples and thermocouple protective sleeves (tubes) for temperature measurement systems, etc.
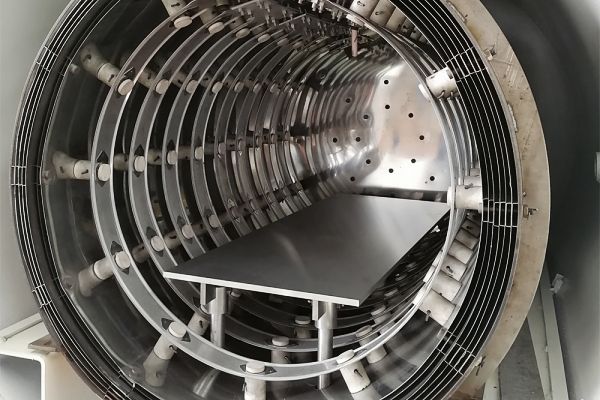
Vacuum Furnace
Vacuum furnaces are mainly used for ceramic firing, vacuum smelting, electric vacuum parts degassing, annealing, metal parts brazing, ceramic-metal sealing, physical vapor deposition (PVD), etc.
We provide heating elements, boats and carriers, heat shields, crucible liners, tungsten wires, and evaporation sources, processed parts, fasteners, etc. The materials are tungsten, molybdenum, or tantalum, which can be customized.
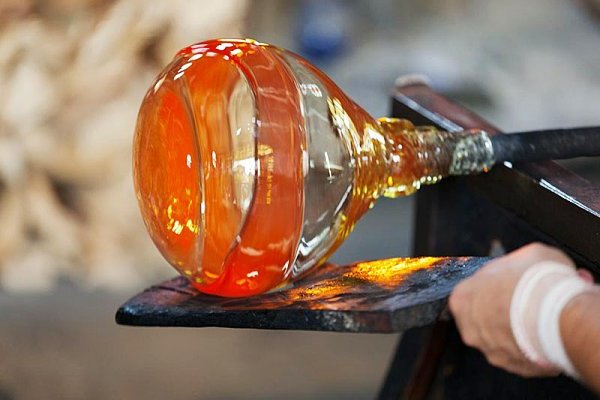
Glass And Rare Earth
› Glass Industry
We provide molybdenum electrodes for glass melting.
Our molybdenum electrodes are made of 99.95% high-purity molybdenum rods.
Molybdenum electrode size: φ20-152*L (unit: mm), we can provide an alkali-washed surface, mechanically polished surface, etc.
› Rare Earth Industry
The rare earth industry involves the extraction, processing, and utilization of rare earth elements, which are important components of various advanced technologies and applications.
We can provide tungsten, molybdenum, and tantalum heating elements, sintered tungsten, molybdenum crucibles, graphite crucibles, etc.
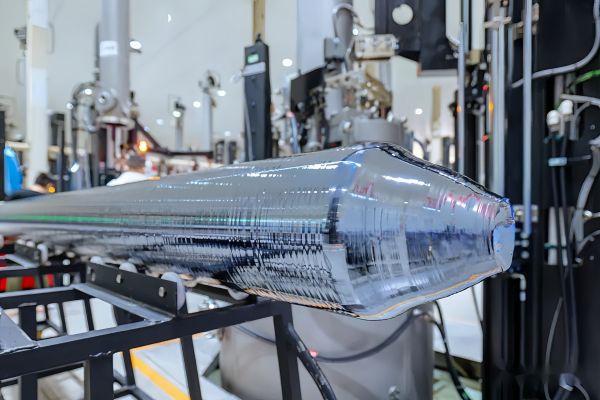
Photovoltaic & Semiconductor
A single-crystal silicon growth furnace, also known as a silicon crystal growth furnace or silicon ingot furnace, is a special equipment used in the photovoltaic and semiconductor industries to produce high-quality single-crystal silicon ingots.
Monocrystalline silicon is the basic material for manufacturing semiconductor devices such as integrated circuits (ICs), solar cells, and sensors.
The "Czochralski method" is currently the most widely used method for preparing single-crystal silicon.
We provide molybdenum seed rods, tungsten and molybdenum crucible liners, fasteners, molybdenum hooks, tungsten carbide hammers, etc.
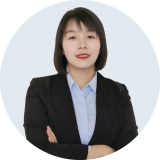
Contact Us
Amanda│Sales Manager
E-mail: amanda@winnersmetals.com
Phone: +86 156 1977 8518 (WhatsApp/Wechat)
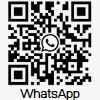
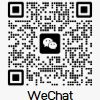
If you would like to know more details and prices of our products, don't hesitate to get in touch with our sales manager (Amanda), she will reply to you as soon as possible (usually no more than 12 hours), thank you.